The QUANTiNO is unloaded. Today is the first test of an electric vehicle powered by a nanoFlowcell without super-capacitors (supercaps). The energy for the electric motors will come directly from the flow cell, without any buffer storage in between. Should the test set-up nanoFlowcell à electric motor also function as expected under "stress", this would mark a further milestone in the development of automotive flow-cell drives.
Accelerating Change – QUANTiNO in the Fast Lane
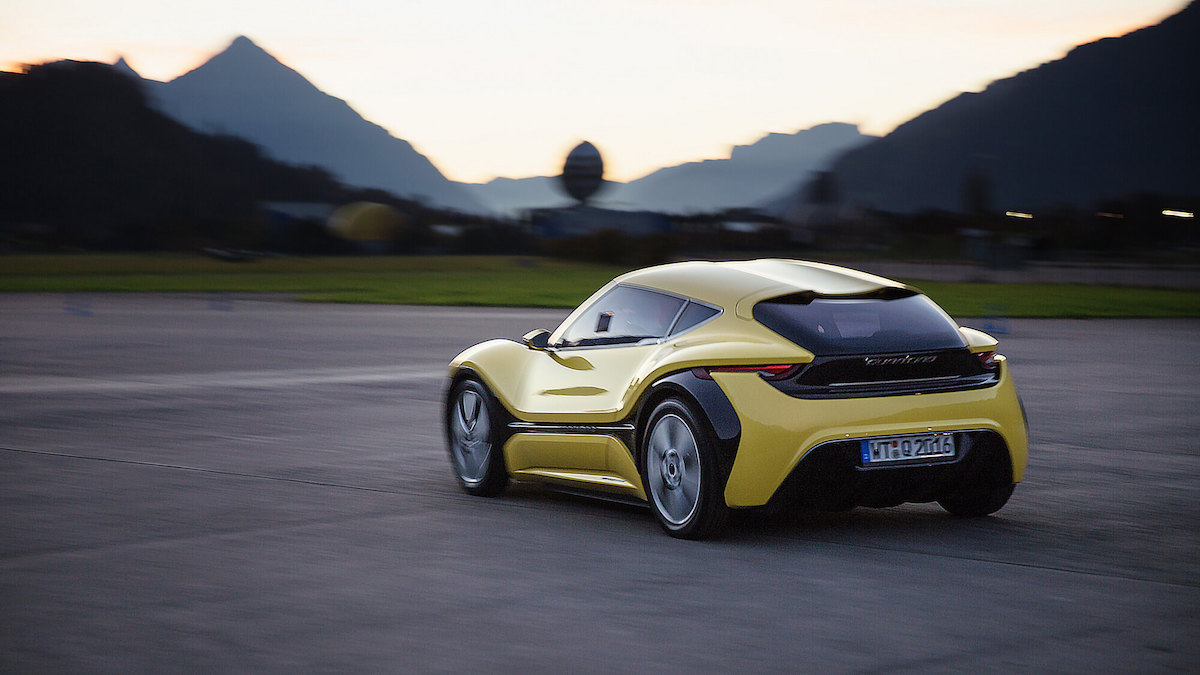
The nanoFlowcell test crew arrives at the former military airfield in Interlaken. It's a remote facility, with virtually no traffic on the roads round about, meaning only very few onlookers will be around. The airfield consists of a straight around two kilometres in length with large turning radii at the top end of the strip - unusual, but sufficient for the spontaneously organised, unplanned test drive with the QUANTiNO.
The surrounding snow-covered mountains are the perfect backdrop - but it's unfortunately also very fresh. Winter is, after all, just around the corner and, despite the sunshine, the outside temperatures don't climb above a rather frosty four degrees Celsius.
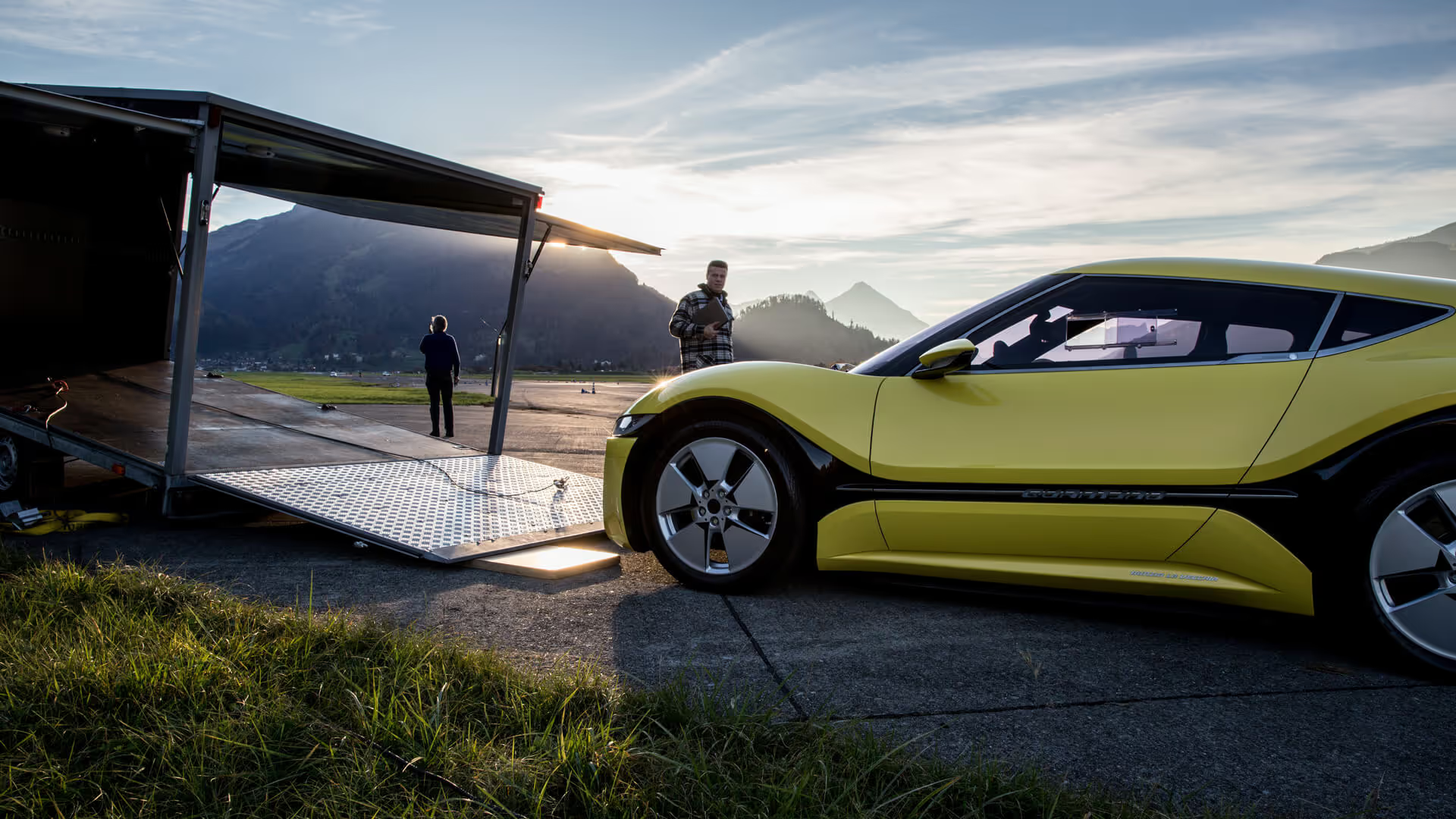
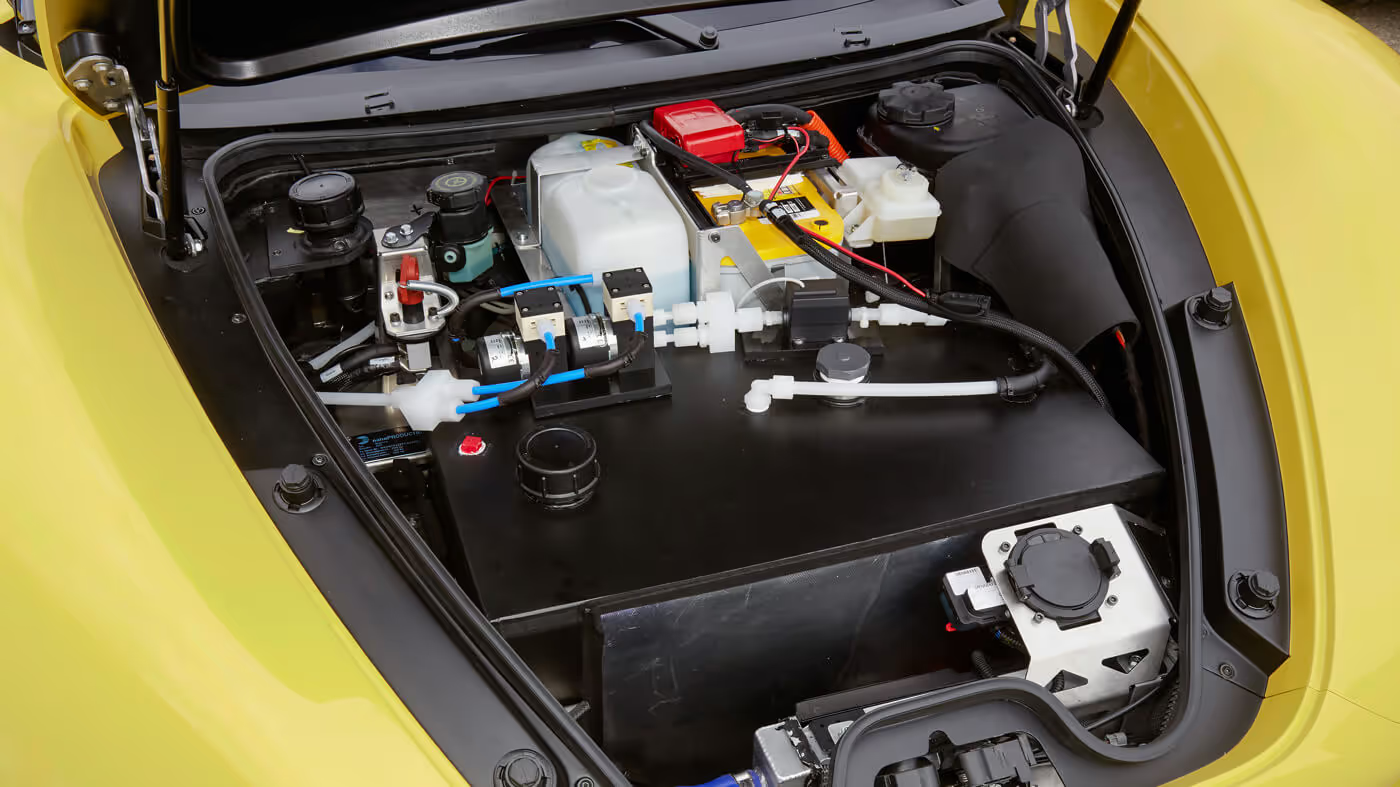
Research has been ongoing for years into this simplified and more cost-effective solution, but simulations have always indicated unsatisfactory results with the kind of test configuration that would be required in practice with a prototype. However, the last few weeks have been fraught with issues associated with the control software for the supercaps in the QUANTiNO. So the decision was taken to circumvent the supercaps within the system. After all, the test vehicle is an important research platform for the further development of the nanoFlowcell and should remain operational under all circumstances.
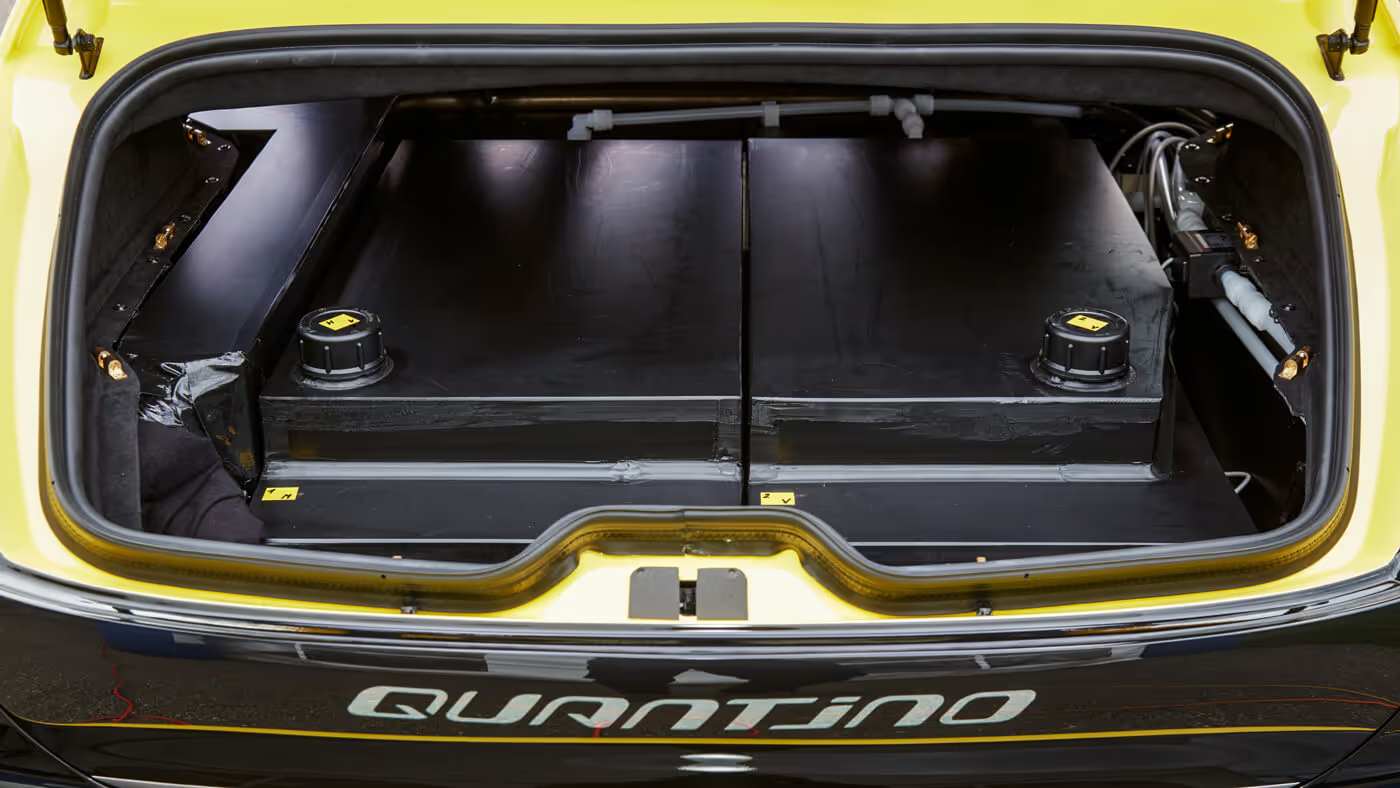
But why were these supercaps used in the first place? Supercaps are used in the QUANTiNO to regulate the energy flow during acceleration and driving. So far, it has not been possible to regulate the electricity flow in the nanoFlowcell as flow cells have only two modes - "on" (supplying energy) or "off" (not supplying energy). To regulate the electricity flow, e.g. less electricity at lower speeds and more electricity at high speeds, supercaps were incorporated into the system to regulate the flow of electricity to the electric motor in line with the position of the "gas" pedal.
Theoretically, a flow cell in a 48 volt low-voltage system such as the QUANTiNO can also supply energy directly to the electric motors - assuming the power of the flow cell has been adapted to the maximum energy requirements of the drive system. Today will show whether the engineers' theoretical calculations will also deliver the desired results in practice. What the development team wants to examine today is a new and never-before tested configuration. They are prepared to accept lower acceleration characteristics and a lower top speed in return for being able to guarantee the QUANTiNO's ability to participate in further testing with the nanoFlowcell.
The QUANTiNO drives along the runway at speeds of around 150 km/h. Sustained acceleration on the straights, several laps at speeds of around 70 km/h. The flow cell delivers a constant flow of energy. However, not to the supercaps but via a DC/DC transformer directly to the 80 kW electric motor.
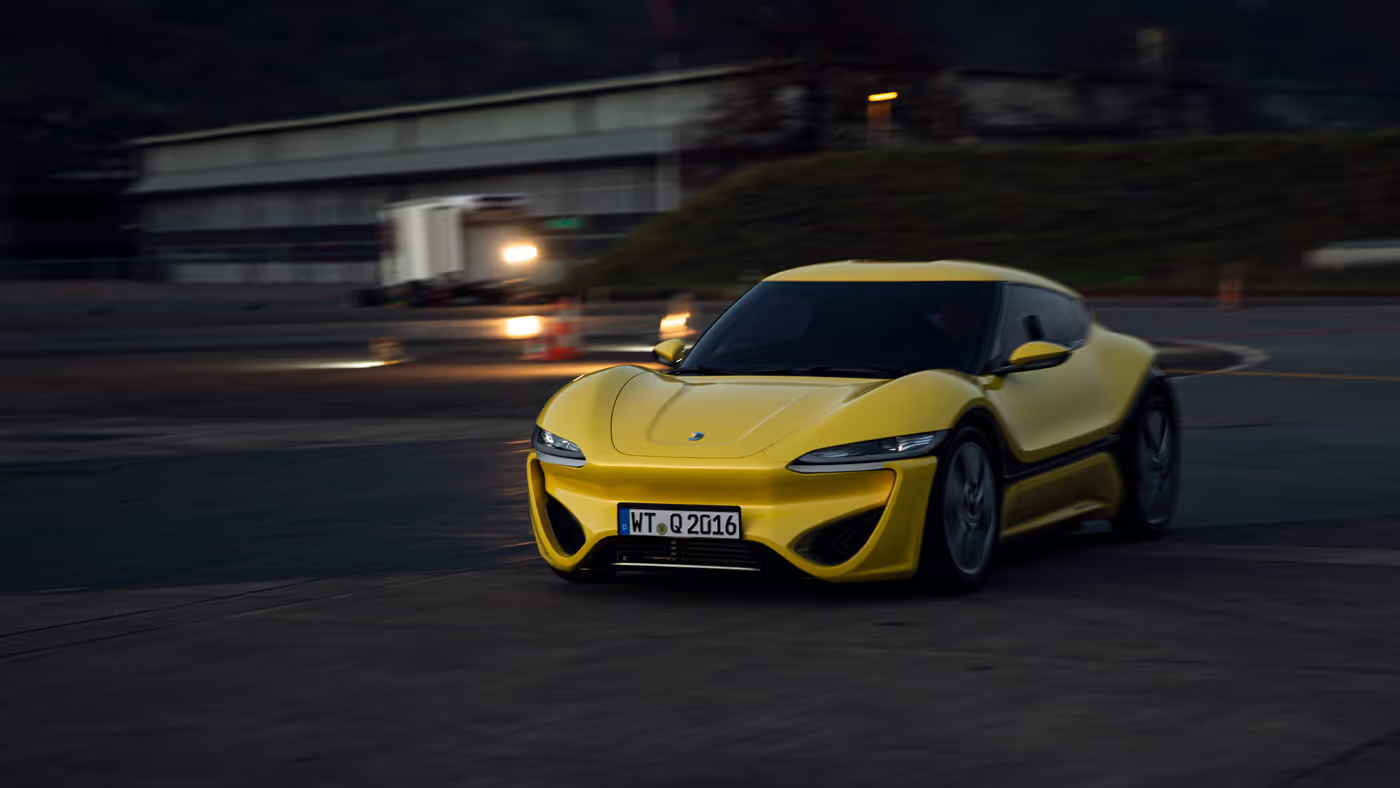
The system is constantly challenged - non-stop. The systems in the QUANTiNO deliver measurement data over a total of more than five hours without interruption, until night falls and the arrival of deer on the strip force a halt to the test drive. At the end of the day, enough measurement data had been gathered to confirm the theoretical calculations - it is possible to use measurement-control technology to manage a fuel cell in an automotive electric drive! To an outsider, this may sound rather succinct, but for the nanoFlowcell development team, QUANTiNO wrote history today - the first drive in an electric car with a flow cell managed through measurement control!
Ultimately, an electric-car system architecture without supercaps means a considerable reduction in weight and cost. It marks an engineering milestone in the development of the nanoFlowcell system. Obviously, the development of a nanoFlowcell managed by control technology is far from complete. The evaluation and analysis of the measurement protocols will show the development engineers what they need to do to improve the system in detail.
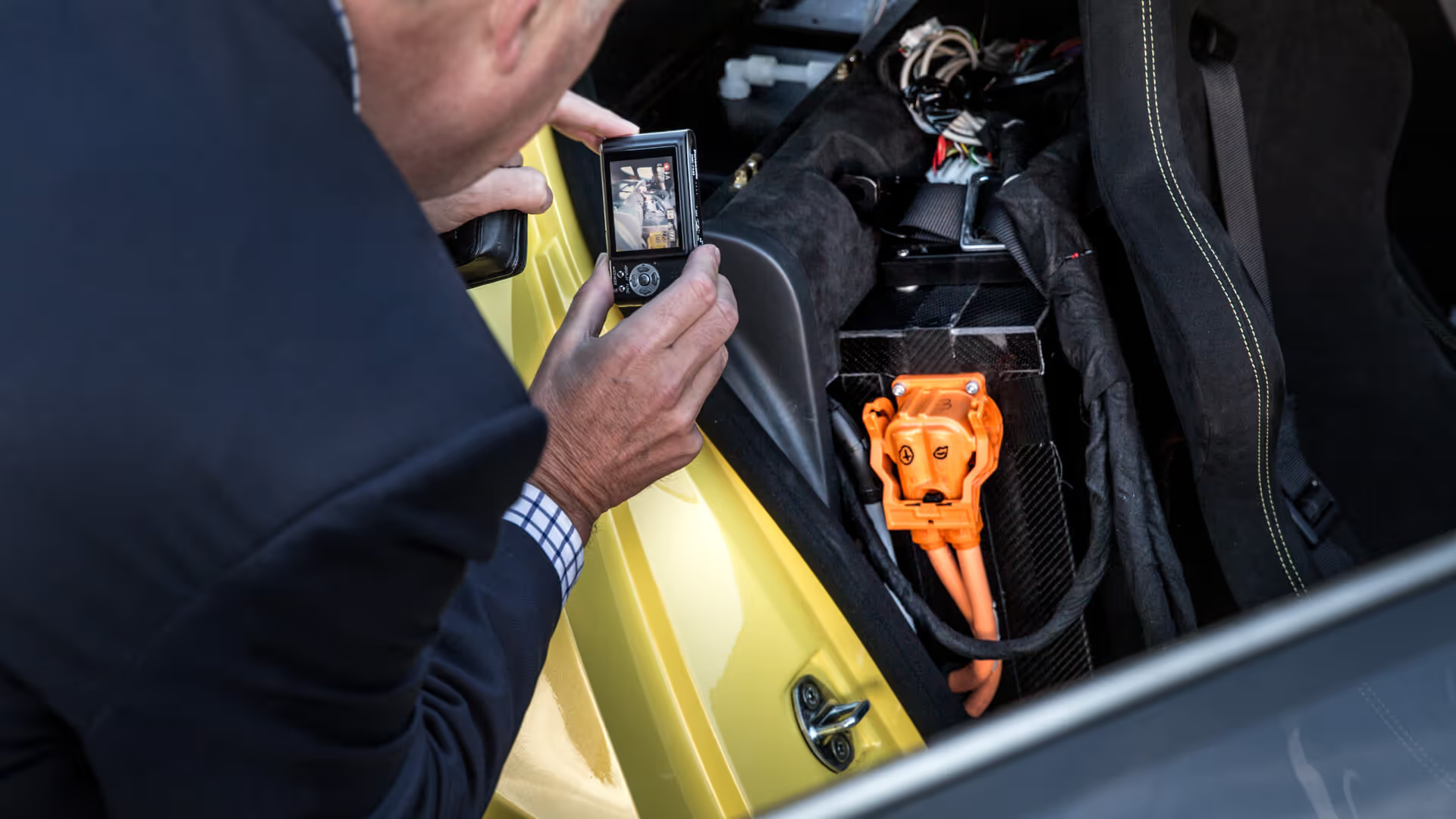
The QUANTiNO is the only road-legal electric vehicle with a low-voltage drive system (48 volts), making it the electric vehicle with the highest possible functional safety. Its nanoFlowcell drive also makes it the most environmentally attractive electric vehicle. By dispensing with the supercaps, the nanoFlowcell low-voltage drive system has been slimmed down to the degree that the weight and production-cost benefits now make the QUANTiNO the most efficient EV concept from an economic standpoint, too.
In terms of effectiveness and efficiency, the nanoFlowcell low-voltage drive system is now overtaking today's internal combustion engines and battery-electric drive systems and is proving itself as a forward-looking approach for the technical design of modern electric vehicles.
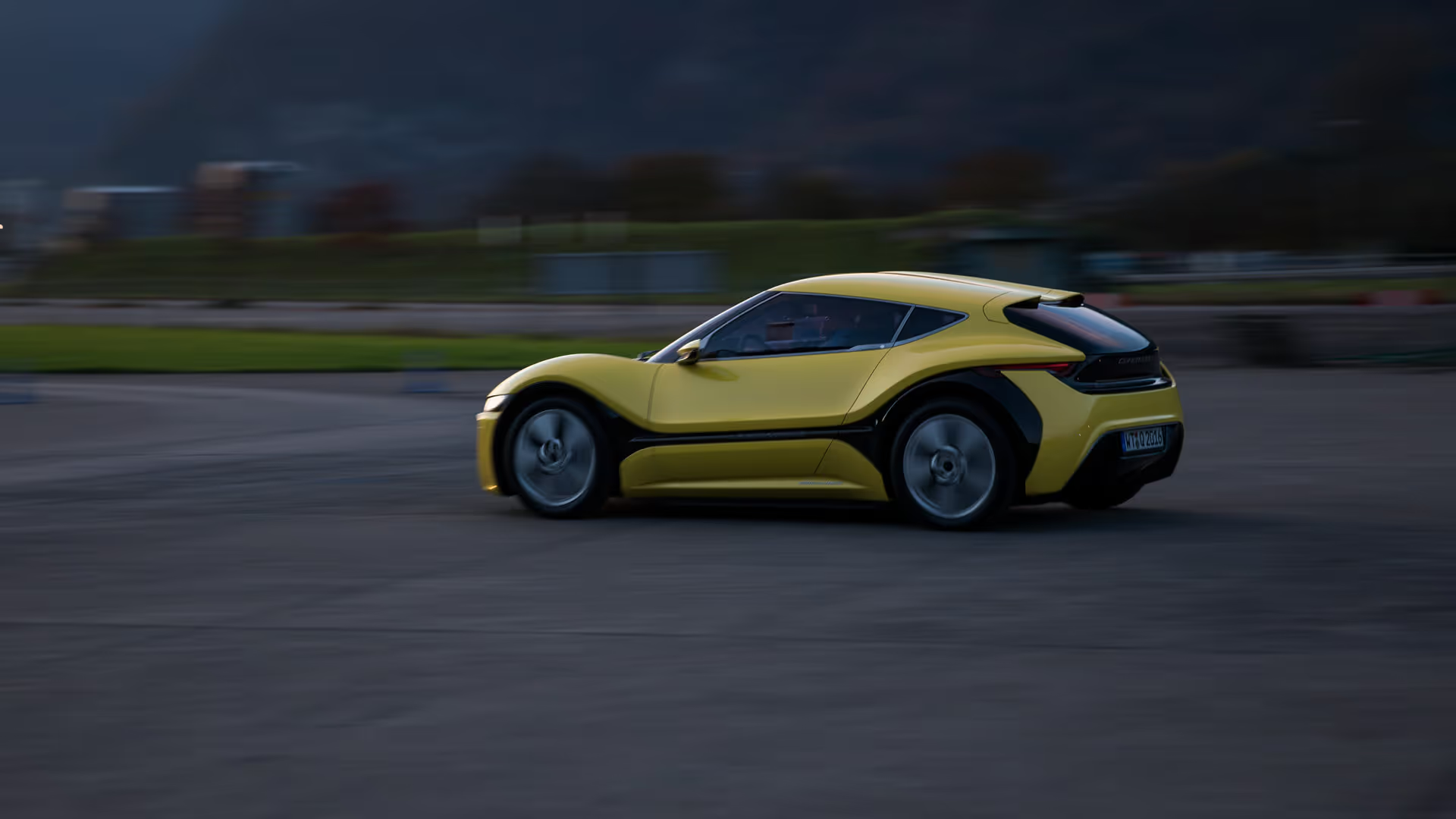